Why Smart Manufacturers Are Moving to Upstate NY
Rising costs, outdated infrastructure, and workforce challenges are driving a new wave of smart manufacturers to rethink where they operate—and many are landing in Upstate New York. What might have once seemed off the radar is now a hotbed of opportunity for companies looking to modernize, save, and scale.
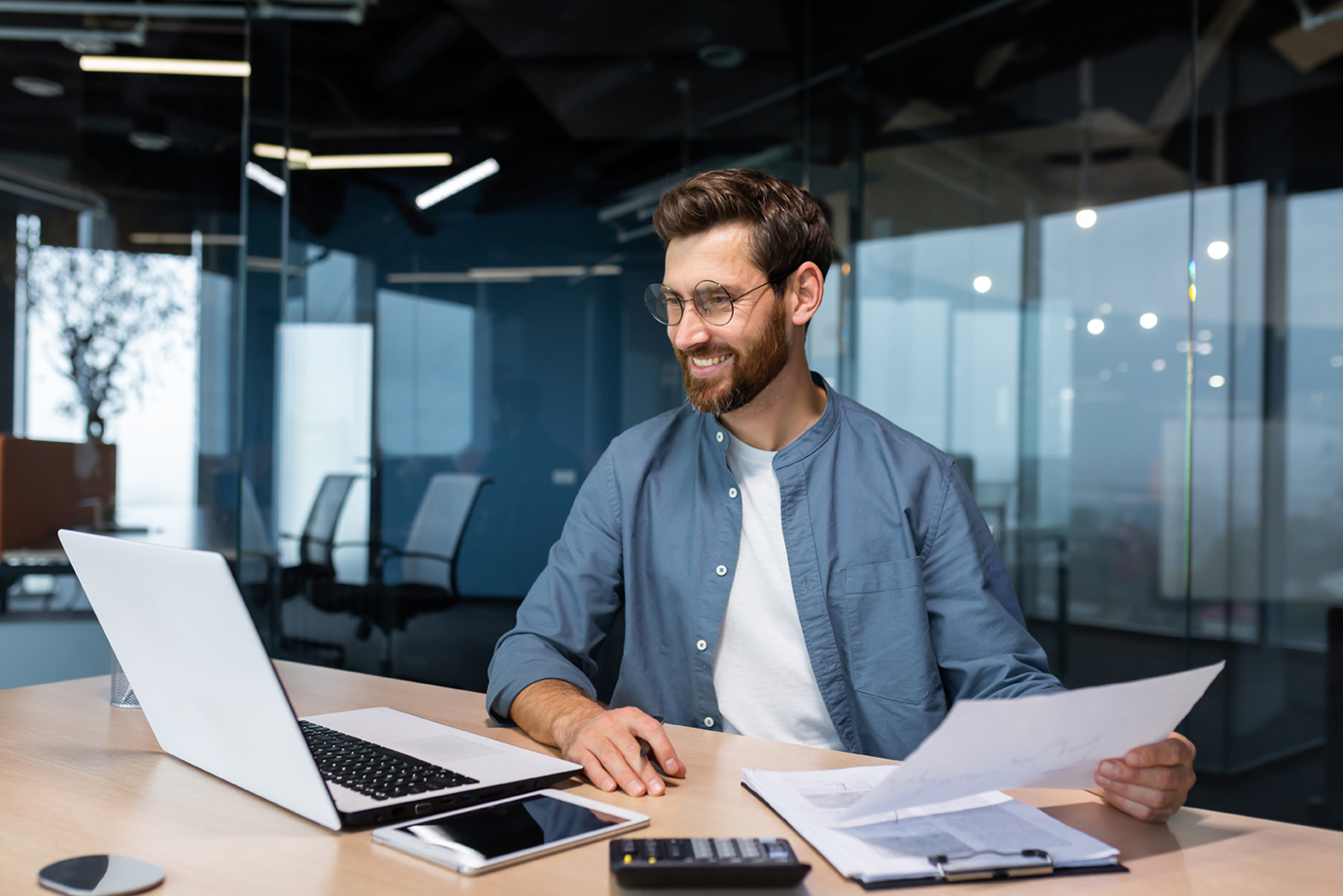
1. Real Savings That Hit the Bottom Line
Smart COOs are finding substantial cost reductions through programs like the FCIDA’s 10-Year PILOT (Payment in Lieu of Taxes), which offers:
50% property tax exemption in year one, tapering over 10 years
8% sales tax exemption on equipment and construction materials
1% mortgage recording tax exemption
For manufacturers managing tight margins and multi-million-dollar relocations, these incentives aren’t perks—they’re game-changers.
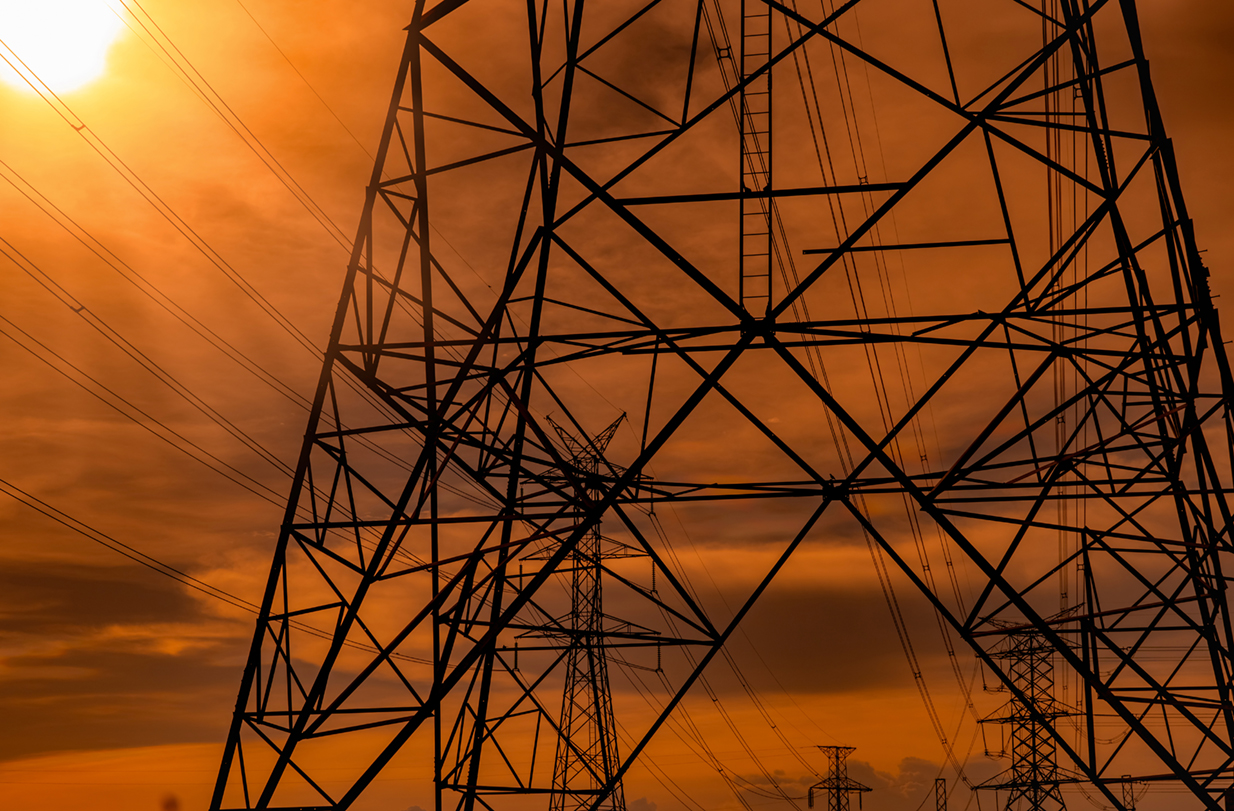
2. Sites That Are Ready—Not Just Promised
Delays kill ROI. FCIDA offers shovel-ready industrial parks like:
These sites come with pre-installed utilities, zoning aligned for industrial use, and streamlined 60–90 day approvals—meaning less red tape, fewer unknowns, and faster time to production.
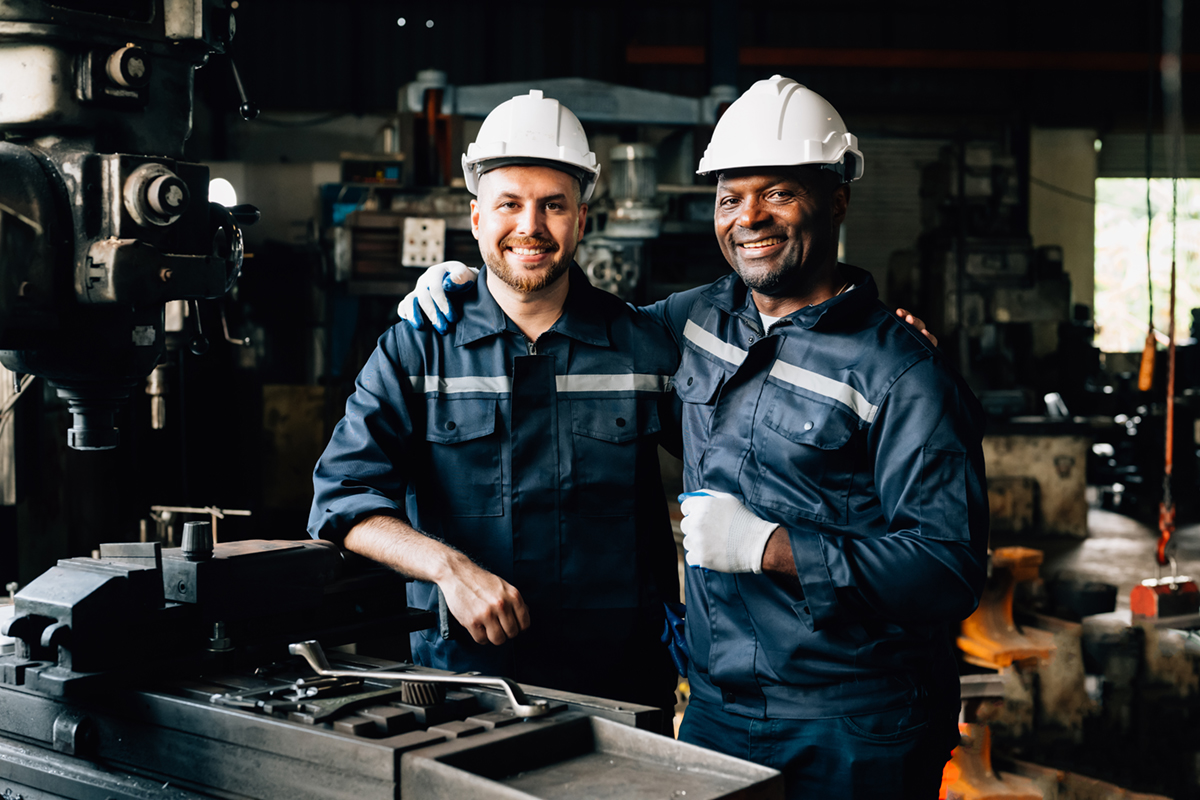
3. Workforce That’s Actually Work-Ready
Forget generic labor pools. Through partnerships with local colleges, FCIDA helps you customize training pipelines aligned to your automation, safety, and production needs. Whether you’re installing advanced robotics or scaling a second shift, the region’s workforce is willing, trainable, and affordable.
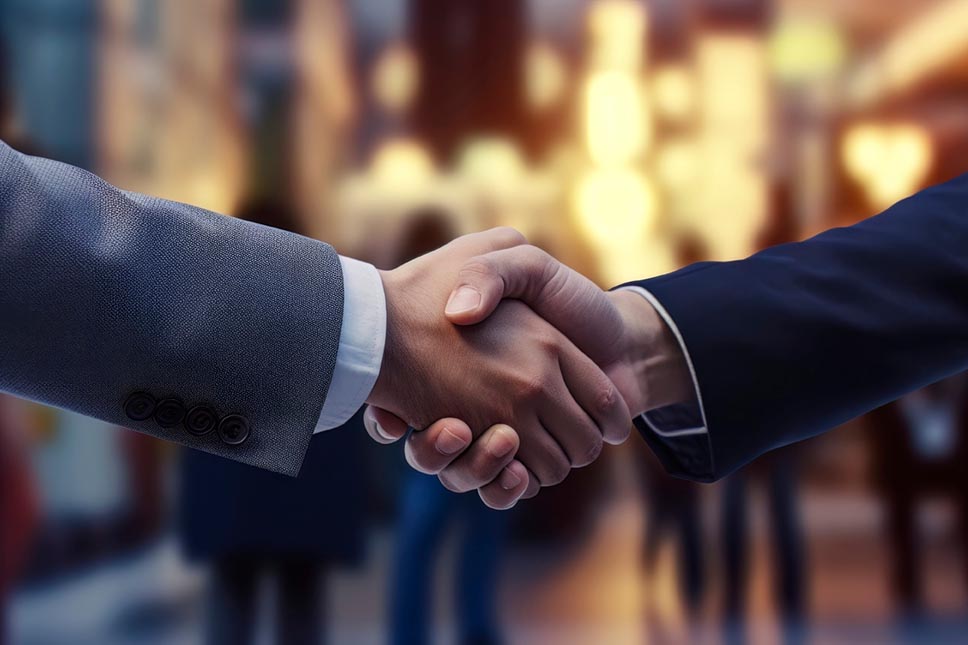
4. Expansion Support Beyond the Ribbon Cutting
Many regions offer front-end help—but disappear once ground is broken. FCIDA takes a longer view:
Local contractor and utility coordination
Workforce onboarding support
Help securing additional grants and workforce credits
Advocacy during phased expansion or adding new lines
It’s true operational partnership, not just real estate sales.
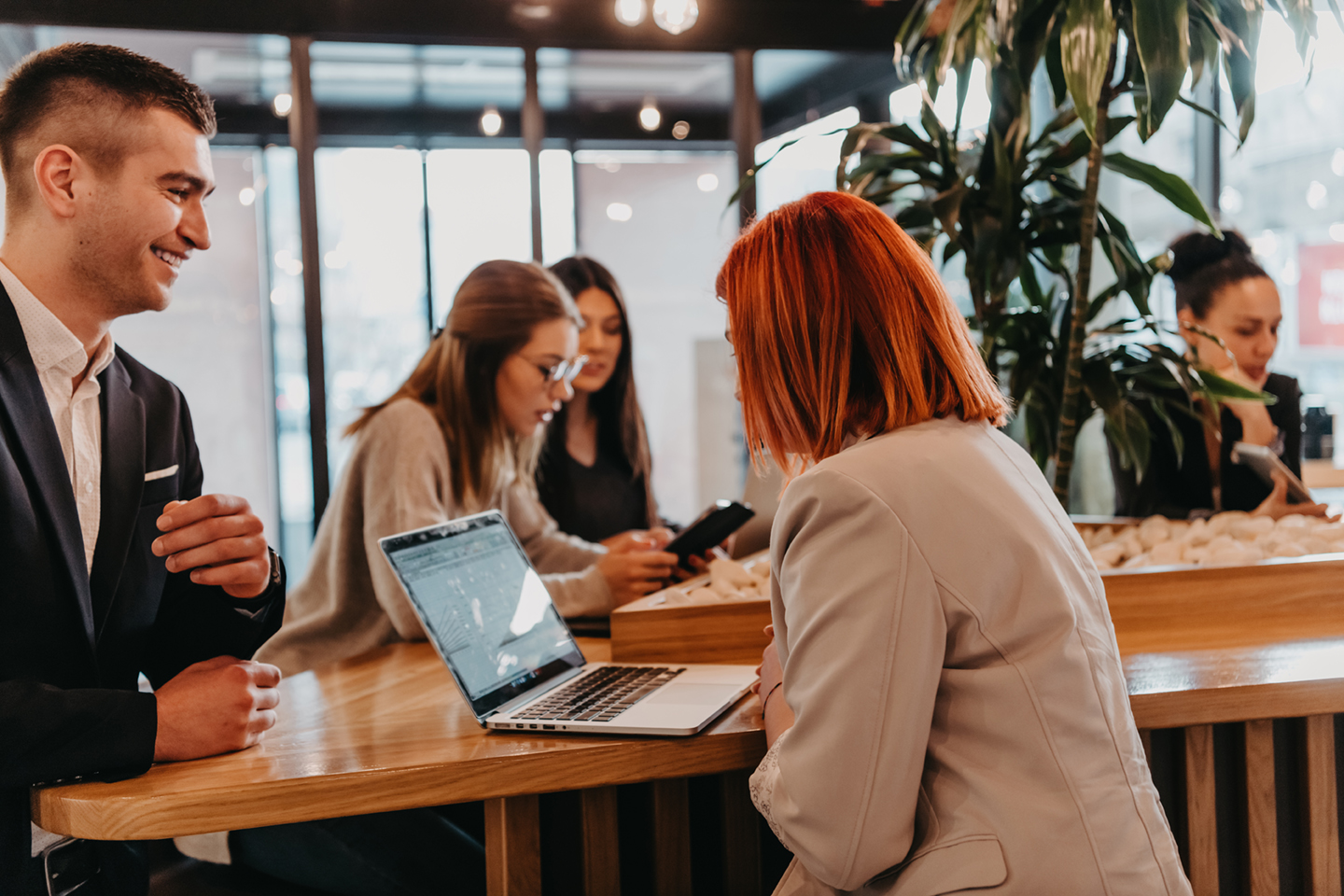
5. A Region Built for Manufacturers
Upstate NY offers what modern manufacturing demands:
Proximity to East Coast supply chains and ports
Reliable power, broadband, and transport logistics
Competitive wages and lower facility costs
A pro-business culture that values industry growth
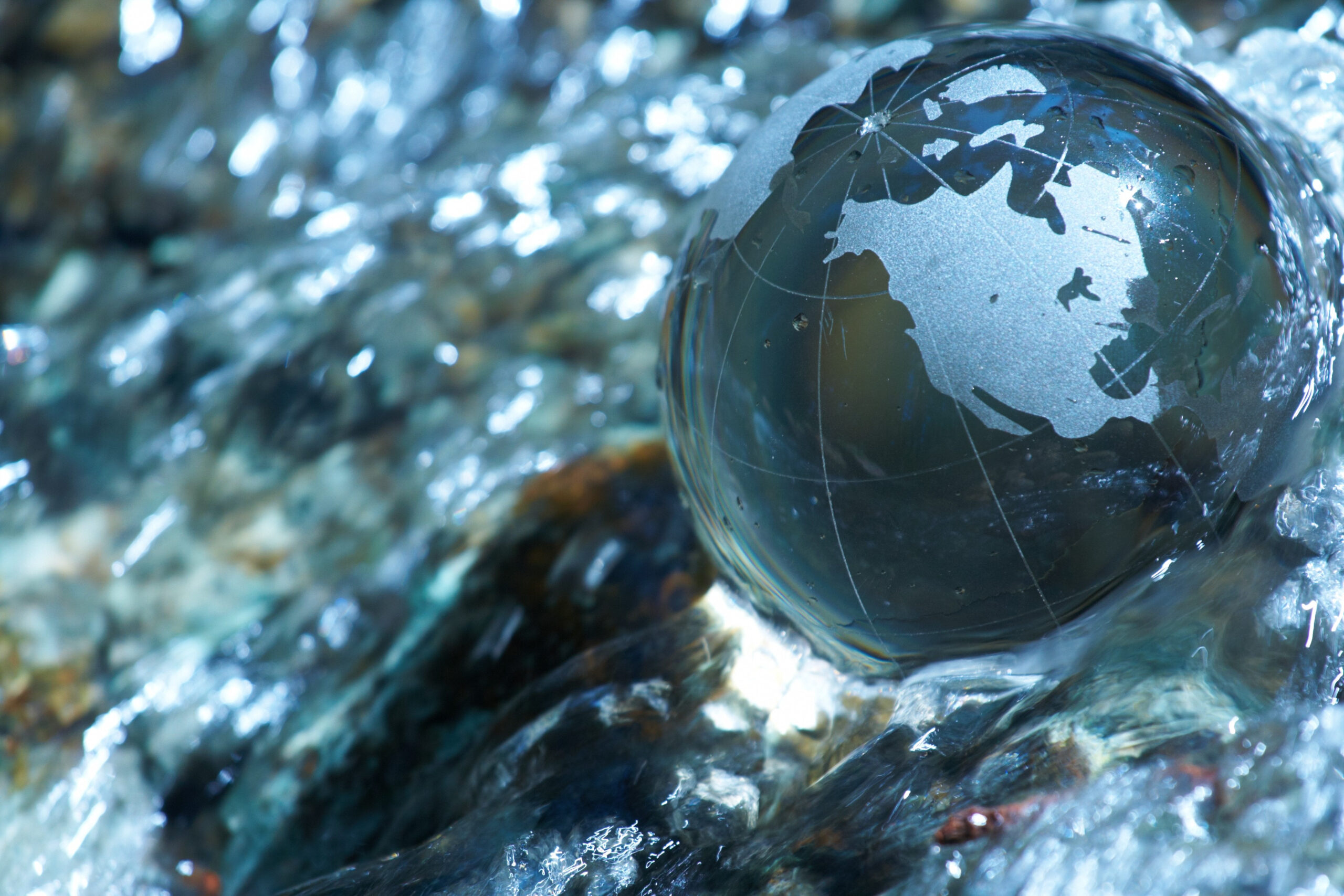
6. Industrial‑Scale Water & Wastewater That Powers Growth
Fulton County NY isn’t just about land and labor—it’s also equipped with industrial-grade water and wastewater systems that large manufacturers and food processors depend on. With access to four reservoirs holding 710 million gallons, Fulton County reliably meets high-volume water demand.
On the wastewater front, the Gloversville–Johnstown Treatment Plant (GJJWTF) processes up to 13.8 M gal/day, operates at just half capacity, and is the only U.S. plant that produces more energy than it consumes, thanks to methane-powered CHP.
For producers in dairy, food‑processing, or biotech, this means direct discharge pipelines, built‑in pretreatment for high‑strength waste (like whey), and significant annual savings—all while supporting sustainability and accelerating permits.
The Bottom Line
Relocation isn’t just about the cheapest land or biggest building—it’s about total cost of ownership, execution certainty, and long-term growth. Smart manufacturers aren’t just moving. They’re moving strategically—and they’re betting on Upstate NY.
Ready to explore shovel-ready sites or run a tax savings scenario?
Get in touch with Fulton County IDA (FCIDA) for a no-cost consultation and customized ROI analysis.